Applications
Tailings Management
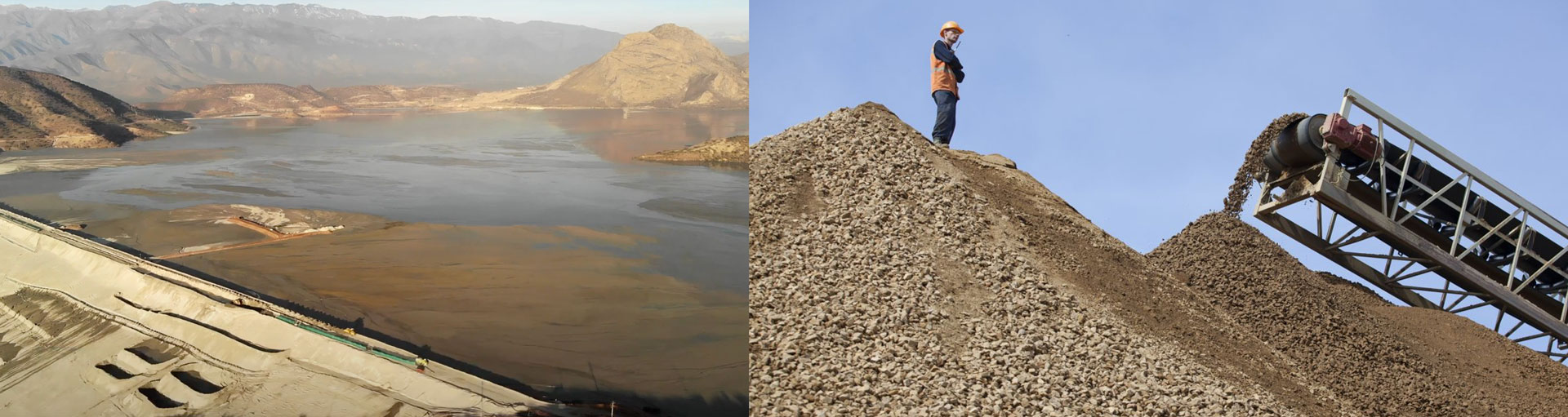
Tailings Management
What are
tailings?
Tailings are the waste material resulting from the different mineral processing plants. As globally the ore grades are falling, to separate & recover valuable minerals like copper, gold, iron, zinc, silver, lead etc. from the mineral ore it is necessary to excavate a big volume of earth. Because the percentage of the desired ore or ore concentrate inside the excavated earth is quite small in comparison to the volume of undesired materials called tailings. As an example in some gold mine the concentration of gold is only 5-10gr 0n 1000.000gr of earth excavated that means that more than 99% of the earth excavated is tailings. For this reasons to separate & recover the valuable minerals like copper, gold, zinc, iron ore etc.. from the mineral ore it is necessary to use a specific physical and chemical process.
The most common mineral processing plants use process like flotation, leaching mainly for copper, gold and zinc concentrate or the magnetic separation like in the case of iron ore mine. During all the mineral processing operations a big volume of process water is required to separate the gold, zinc, copper, iron ore concentrates from the tailings. Also metallurgical plants like the alumina refinery which uses the Bayer process produces a big volume of tailings called red mud.
Especially the red mud tailings are quite dangerous for the environment, because the red mud tailings contain caustic soda. Due to the fine grinding applied during mineral processing the tailings resulting from the mineral and metallurgical processing plant, consists of a slurry of fine particles. The mining sector today is facing the challenge to mange a huge or colossal volume of slurry or sludge tailings that is threatening our environment everyday.
What is tailings management?
The management of slurry tailings is an important challenge the mining sector is facing today. It is necessary to organize the storage of a huge volume of tailings produced from the enrichment plant of copper, gold, zinc, iron ore etc. and it is not easy to store the tailings in a safe way when they are in the form of a slurry. So the tailings management is a complex process, that consists of storing a big volume of copper, gold, zinc, iron ore tailings, in safe way and at the same time to recycle as much as possible the process water to the concentrator plant.
This recycled process water to the concentrator plant can substantially reduce the need of fresh or back up water for the concentrator plant thus making the concentrator more water efficient. Hence the main goal of the tailings management is to develop an efficient solution that allows to store a big volume of mining tailings in a safe way that also allows to recover as much as possible the process water.
What is tailings management?
The management of slurry tailings is an important challenge the mining sector is facing today. It is necessary to organize the storage of a huge volume of tailings produced from the enrichment plant of copper, gold, zinc, iron ore etc. and it is not easy to store the tailings in a safe way when they are in the form of a slurry. So the tailings management is a complex process, that consists of storing a big volume of copper, gold, zinc, iron ore tailings, in safe way and at the same time to recycle as much as possible the process water to the concentrator plant.
This recycled process water to the concentrator plant can substantially reduce the need of fresh or back up water for the concentrator plant thus making the concentrator more water efficient. Hence the main goal of the tailings management is to develop an efficient solution that allows to store a big volume of mining tailings in a safe way that also allows to recover as much as possible the process water.
Tailings Management Methods
The tailings can be managed in different ways depending on the physical and chemical characteristics of the slurry, the mine site topography, climatic condition, water availability and local environmental regulations. The most common and old tailings management method is the Tailings Management Facility (TMF) or the Tailings Storage Facility (TSF) where the tailings slurry is stored in huge tailing dams (tailings facility).
The slurry tailings used to be pumped to the tailings facility directly from mineral processing plant where the concentration of solids in the slurry for example in the case of the flotation process is typically 15-30%. Whereas when there is an intermediate thickening step, the tailings before to be sent to the tailings dam go to an equipment called high rate thickener. The high rate thickener enables to increase the concentration of solids from 15-30% to 45-55% depending on the type of thickener used and from the nature of the tailings.
In this way it is possible to reduce the volume of tailings that must be stored in tailings facility and to recover an important volume of water, because high rate thickener is an equipment designed to perform solid liquid separation by sedimentation process.
Another intermediate technology used in order to improve and optimize the tailings management facility method has been the paste technology. By this technology instead of high rate thickener another equipment called paste thickener is used. In theory paste thickener allows to increase the concertation of the solids in the tailings slurry up to 70%.
We said in theory because even if the paste thickener can reach a concentration of solids up to 70%, but usually after 60-65% of concentration it is almost impossible to pump the sludge / paste produced from the paste thickener to the tailings facility. So practically most of the tailing management facility that uses the paste technology works at a concentration of solid in the tailings only 10% higher than the high rate thickener.
So by the paste technology it can be possible to improve the life of the tailings management facility but in any case it is necessary to use a tailings pond for the storage of the concentrated slurry tailings. Moreover the paste technology have also quite high CAPEX and OPEX cost. For these reasons nowadays this technology is not so much preferred & used.
After the storage of the slurry tailings in tailings dam it is necessary to wait for the natural settling of the solid material in order to recover as much as possible water and to get a drier solid. Unfortunately in recent times we have seen some catastrophic failures of large tailing dams with disastrous consequences resulting death to people and serious damage to the environment. So in spite of all the effort to build tailings facility according to the Global Industrial Standard on Tailings Management the risk to manage the tailings by tailing management facility or tailing dam remains quite high, because there are situation that nobody can forecast such as exceptional rains or earthquake. These natural phenomenon are quite common today with fast changing of the global climate conditions. This new and unpredictable situations stresses a lot the tailings dam which can result in catastrophic failure of the tailing management facility.
Another tailings management method is the mine back fill where the tailings will be sent back to the mine. It can be used in the open pit mine or even underground mine but the use of this method is linked to the specific situation and conditions of the mine. So in most of the case it is not applicable.
The new approach to Tailings management is Dry Stacking. This new approach to the tailings management is based on the principles of:
- to eliminate all the risk associated with the slurry tailing management (Tailings dam failure) and
- to recover as much as possible water in constant way
These principles are driving the development & implementation of the new technology called dry stacking method of tailings management.
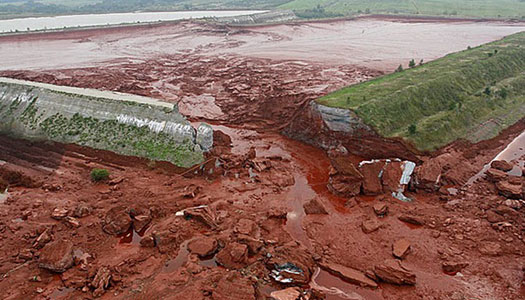
Red Mud Tailings Dam Failure in Alumina Refinery
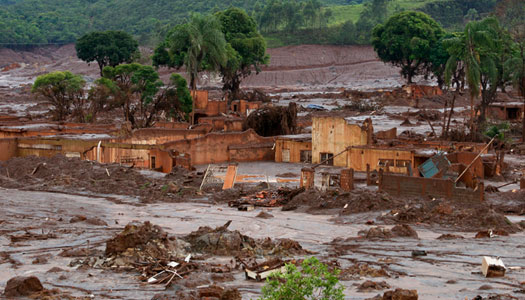
Iron ore Tailings dam failure in Brazil
What is dry stacking?
The tailings management by the dry stack technology consists of dewatering of the slurry tailings by filtration technology. And after the filtration or dewatering process to dry stack the dewatered tailing that it is now in the form of dry filtered cake (in solid form) to store safely in stacks.
So the tailings management by dry stacking method is the unique technology that allows us to eliminate the tailings dam. And subsequently it eliminates all the associated risks of the failure of slurry tailings facilities and dams. For dry stacking, the equipment used for the slurry tailings filtration or the slurry tailings dewatering is the filter press. It can be membrane filter press or chamber filter press depending upon the slurry characteristics.
Therefore in the slurry tailings management with dry stacking process forecasts and adds an intermediate step of dewatering the slurry tailing after the thickening phase. During this important slurry tailings dewatering step the filter press simultaneously separates the solids & liquids. This recovered water from the slurry tailings will be recycled back to the concentrator plant making the concentrator more water efficient. And the dry filtered tailings in the form of dry cake will be transported by conveyor system for the safe storage in the dry tailings disposal area.
What is dry stacking?
The tailings management by the dry stack technology consists of dewatering of the slurry tailings by filtration technology. And after the filtration or dewatering process to dry stack the dewatered tailing that it is now in the form of dry filtered cake (in solid form) to store safely in stacks.
So the tailings management by dry stacking method is the unique technology that allows us to eliminate the tailings dam. And subsequently it eliminates all the associated risks of the failure of slurry tailings facilities and dams. For dry stacking, the equipment used for the slurry tailings filtration or the slurry tailings dewatering is the filter press. It can be membrane filter press or chamber filter press depending upon the slurry characteristics.
Therefore in the slurry tailings management with dry stacking process forecasts and adds an intermediate step of dewatering the slurry tailing after the thickening phase. During this important slurry tailings dewatering step the filter press simultaneously separates the solids & liquids. This recovered water from the slurry tailings will be recycled back to the concentrator plant making the concentrator more water efficient. And the dry filtered tailings in the form of dry cake will be transported by conveyor system for the safe storage in the dry tailings disposal area.
What are the advantages and limits of tailings management with dry stacking?
As we have seen tailings management by dry stacking technology looks highly prospective solution for the mining sector. So let’s analyse in more detail what are the advantages of the tailings management by dry staking methods and may be if there is any limitation:
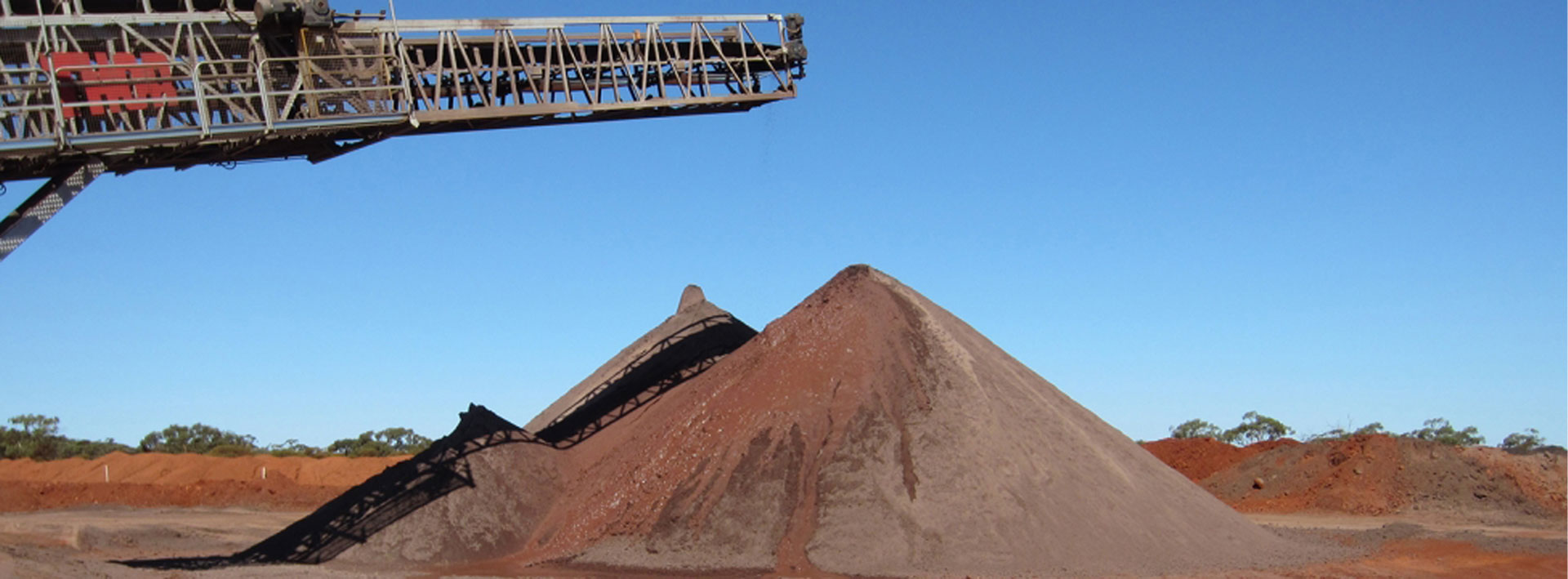
Advantages:
- Green & most environment friendly tailings management solution;
- Zero risk of slurry tailings Dam failure with consequential environmental disaster;
- Zero risk of industrial water going inside the soil or pass through the soil and to contaminate river, lake or some underground drinking water line.
- High water recovery thanks to the filter press technology. Almost 85-90% of the total water used in the mineral processing plant can be recycled. This is very important for regions where the water availability is low and cost of water is high. But above all it limits the use of fresh water for mineral processing. And as we know water is an important limited resource of our planet.
- Constant water recovery & easy and efficient water management for the mining plant.
- Tailings dewatering and filtration plant with dry tailings disposal area have smaller foot print in comparison to conventional slurry tailings dam, so less environmental impact (usually the tailings dam occupies more than 50% of the total mining plant site)
- Zero environmental risk even in the high seismic zone (mining sites are typically in seismic zone)
- Possible to use the dry stack solution even in territory with complicated morphology like in the mountains;
- The best solution for very cold area where the water gets frozen in short time like in the arctic area.
- Tailings dry stack area can be recovered and transformed into a green area while the mining activity stops.
After considering so many advantages for the environment and health & safety of the people around the mining areas, one question arises:
Why not all the mines use the tailings management with dry stacking process today?
The main reason all the mines do not use the tailings management with dry stacking solution is purely economical. In fact if we make a pure economical comparison between the method of tailings management with conventional tailings dam facility and the method of tailings management with dry stacking,
and if we exclude the huge consequential cost linked to the risk of the tailings dam failure and its cost impact on the environment, the tailings management with conventional tailings dam is the cheaper method.
The main reason that make tailings management by dry stacking method expensive is the capital investment (CAPEX) of the filter press and its running operating expenses (OPEX) cost.
- Green & most environment friendly tailings management solution;
- Zero risk of slurry tailings Dam failure with consequential environmental disaster;
- Zero risk of industrial water going inside the soil or pass through the soil and to contaminate river, lake or some underground drinking water line.
- High water recovery thanks to the filter press technology. Almost 85-90% of the total water used in the mineral processing plant can be recycled. This is very important for regions where the water availability is low and cost of water is high. But above all it limits the use of fresh water for mineral processing. And as we know water is an important limited resource of our planet.
- Constant water recovery & easy and efficient water management for the mining plant.
- Tailings dewatering and filtration plant with dry tailings disposal area have smaller foot print in comparison to conventional slurry tailings dam, so less environmental impact (usually the tailings dam occupies more than 50% of the total mining plant site)
- Zero environmental risk even in the high seismic zone (mining sites are typically in seismic zone)
- Possible to use the dry stack solution even in territory with complicated morphology like in the mountains;
- The best solution for very cold area where the water gets frozen in short time like in the arctic area.
- Tailings dry stack area can be recovered and transformed into a green area while the mining activity stops.
After considering so many advantages for the environment and health & safety of the people around the mining areas, one question arises:
Why not all the mines use the tailings management with dry stacking process today?
The main reason all the mines do not use the tailings management with dry stacking solution is purely economical. In fact if we make a pure economical comparison between the method of tailings management with conventional tailings dam facility and the method of tailings management with dry stacking,
and if we exclude the huge consequential cost linked to the risk of the tailings dam failure and its cost impact on the environment, the tailings management with conventional tailings dam is the cheaper method.
The main reason that make tailings management by dry stacking method expensive is the capital investment (CAPEX) of the filter press and its running operating expenses (OPEX) cost.
How our modern engineering and smart solution can make tailings management with dry stacking affordable?
For all the reasons & advantages we discussed here, Dewater Filter Press have the goal to motivate the mining sector to implement this excellent solution as a standard of sustainable and safe mining practices.
To support the tailings management by dry stacking solution, our founders with more than 25 years of filtration experience has developed The Next Generation of Filter Press called Dewater HP 4X4 (High Performance Filter Press).
The Dewater HP filter press has all the specific design characteristics for the tailings management. The Dewater HP filter press thanks to its special design and its exclusive modern engineering is able to offer:
- Top pressure filtration performance
- Can dewater a big volume of slurry tailings
- Cheaper CAPEX & OPEX cost than the rest
By these three key points Dewater HP filter press is able to satisfy the interest of the mining sector and its immediate need of sustainable & safe mining practices.
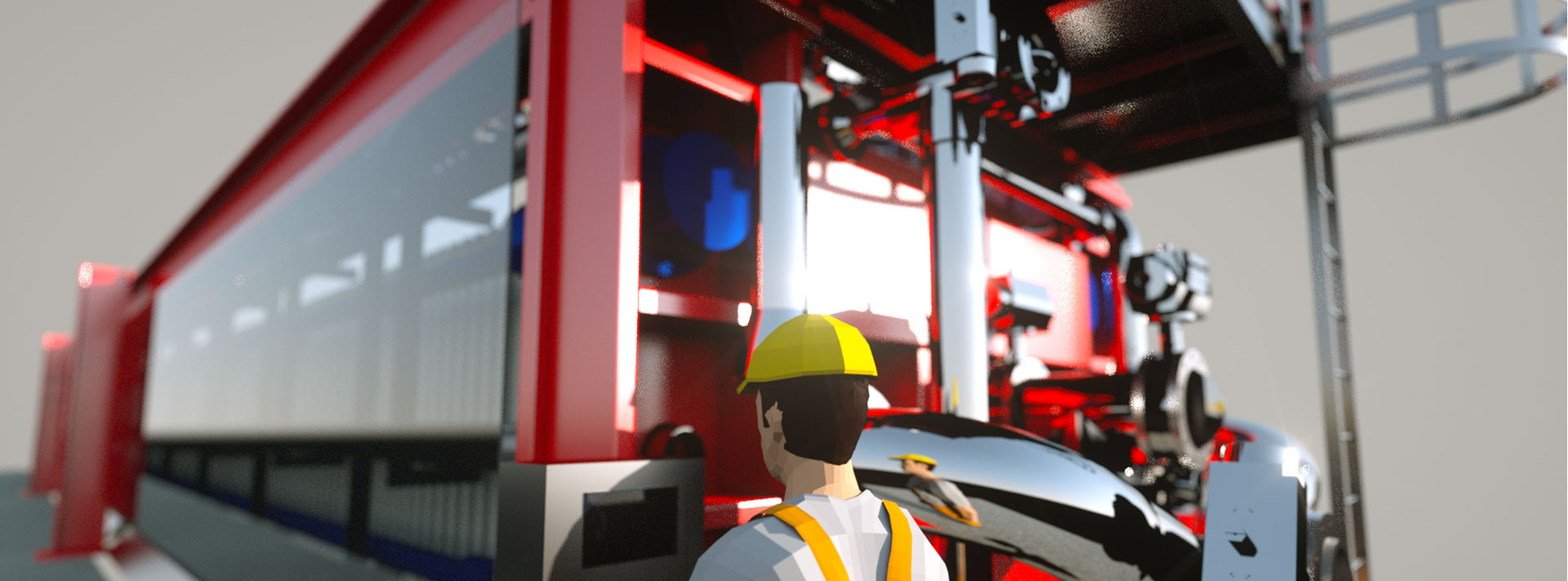
Dewater Filter Press MAS HP 6×6 and Dewater HP 4×4.
The Future is Now
How our modern engineering and smart solution can make tailings management with dry stacking affordable?
For all the reasons & advantages we discussed here, Dewater Filter Press have the goal to motivate the mining sector to implement this excellent solution as a standard of sustainable and safe mining practices.
To support the tailings management by dry stacking solution, our founders with more than 25 years of filtration experience has developed The Next Generation of Filter Press called Dewater HP 4X4 (High Performance Filter Press).
The Dewater HP filter press has all the specific design characteristics for the tailings management. The Dewater HP filter press thanks to its special design and its exclusive modern engineering is able to offer:
- Top pressure filtration performance
- Can dewater a big volume of slurry tailings
- Cheaper CAPEX & OPEX cost than the rest
By these three key points Dewater HP filter press is able to satisfy the interest of the mining sector and its immediate need of sustainable & safe mining practices.
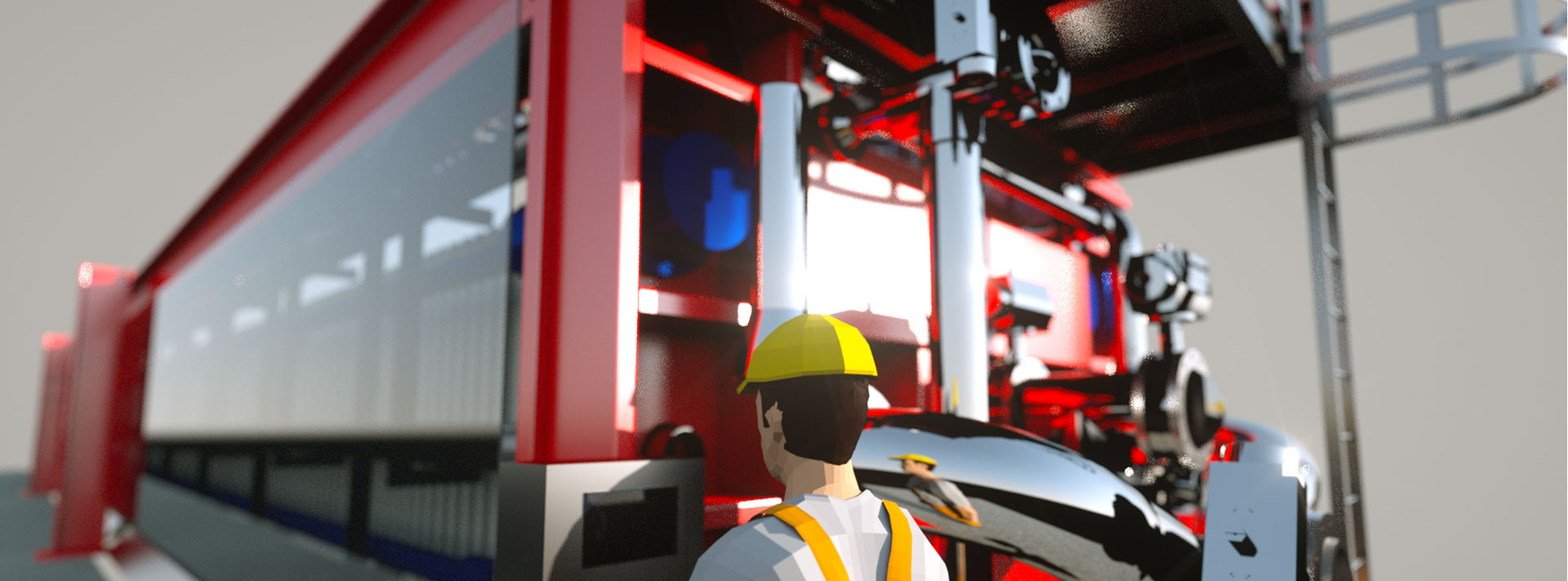
Dewater Filter Press MAS HP 6×6 and Dewater HP 4×4.
The Future is Now
Tailings Management solutions for specific minerals
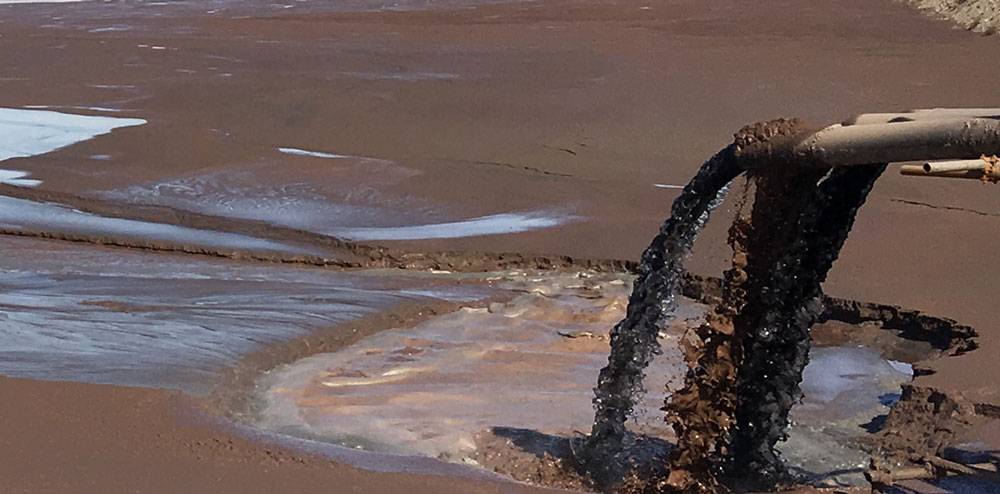
Iron Ore Tailings Filtration
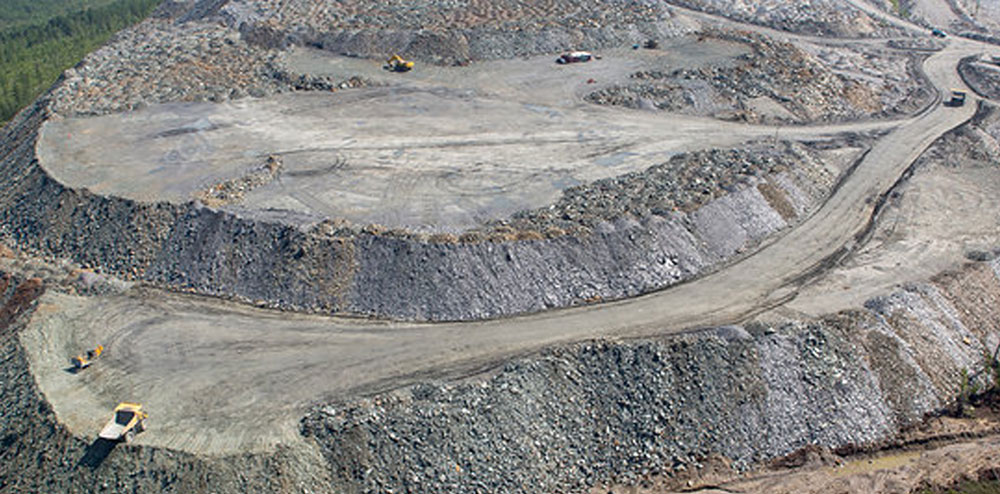
Gold Tailings Filtration
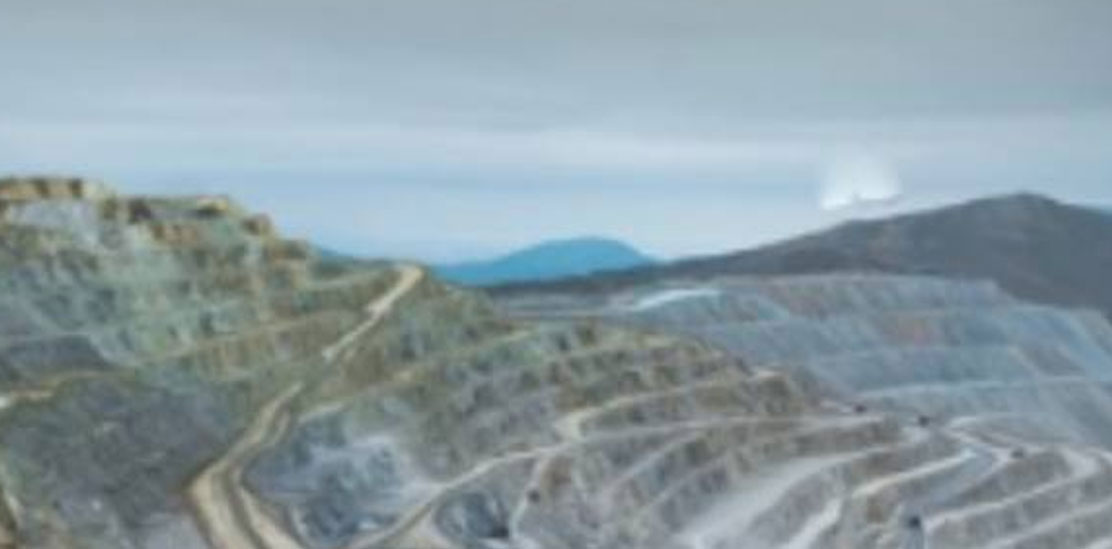